Ingots
Ingots are blocks of metal which are cast into a particular shape. They can vary greatly from metal to metal and from production site to production site. Aluminum, lead, zinc and tin are very often transported in this form.
|
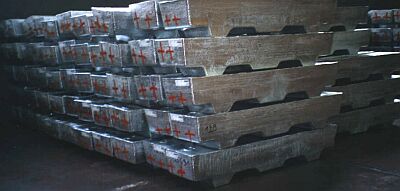 |
|
Loosely stacked tin ingots in storage |
Individual bars are very often stacked at right angles to one another and bundled for transport.
It may be suspected that this cargo was stowed on the basis of the age-old argument, "This cargo's so heavy, it will never slip!". However, it takes more than constant repetition of such erroneous ideas to overcome the laws of physics.
 |
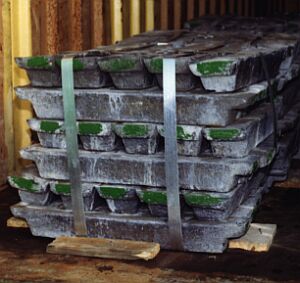 |
|
"Securing" with lengths of board nailed in front |
Packing of this 20' container has been carried out with complete disregard for all the basic rules of stowage. The large gaps in the stow and the considerable mass of the ingots are capable of jeopardizing the container and the means of transport.
 |
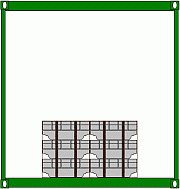 |
 |
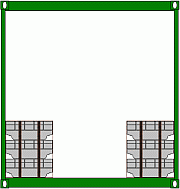 |
|
Centrally packed ingots |
|
Laterally packed ingots |
It is not incorrect, just uneconomic, to pack ingots centrally, as considerably more effort is required to secure them than if they are packed against the sides of the container. If the gap in the stow is left in the center of the container, more than half the cargo securing material can be saved.
|
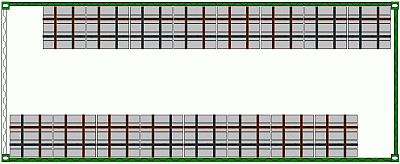 |
|
Laterally packed ingots - plan view |
Ideally, transport modules should correspond to fractions of the internal container dimensions, but that is not the case here. The cargo has thus been packed so that bracing can be provided behind the first door leaf to be closed. On the side of the door leaf to be closed last, the cargo is packed in such a way that it can be blocked at the end face.
|
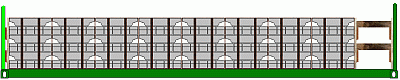 |
|
Side view of right-hand row of ingots bundles - door light green |
|
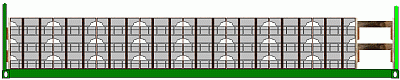 |
|
Side view of left-hand row of ingot bundles - door light green |
|
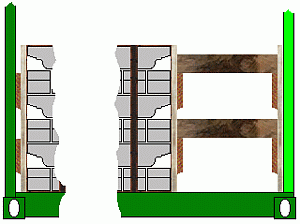 |
|
Detail of lengthwise securing |
If narrow lengthwise gaps remain on the right-hand door side, they are filled with a lattice of two boards nailed to one another crosswise. The large lengthwise gaps are braced. Bracing is provided by two of the above-described lattices, between which two squared lumber members are fitted at top and bottom.
|
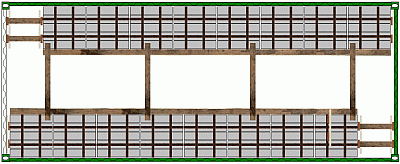 |
|
Bracing of transverse gaps - plan view |
The large transverse gaps are braced with squared lumber members fitted lengthwise and crosswise as shown in the diagram.
|
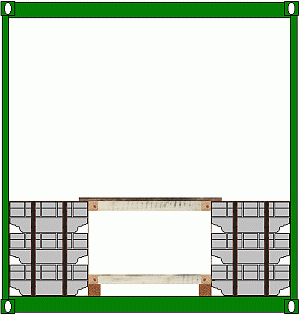 |
|
Bracing of transverse gaps - cross-section |
|
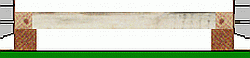 |
|
Bracing of transverse gaps - detail of lower part |
The bracing can be produced very quickly by laying a squared lumber member along the entire length of the lower edge of the internal sides of the bundles. A second squared lumber member of a smaller edge length is placed on top and the space between is braced in the crosswise direction with squared lumber members or beams which are cut to size.
|
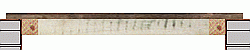 |
|
Bracing of transverse gaps - detail of upper part |
The bracing for the upper part can be prefabricated outside the container. Two squared lumber members are laid out lengthwise in accordance with the bundle position. The space between is filled with transverse squared lumber members. Boards, which overhang slightly on each side, are nailed onto the crosswise and lengthwise wooden members. The whole structure is suspended in the gap.
|
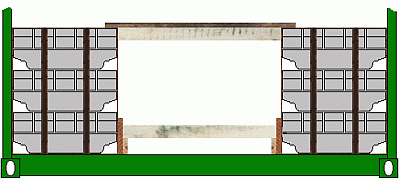 |
|
Bracing of transverse gaps - simpler variant |
If the ingots are well bundled, crosswise bracing consisting in the lower part of boards nailed together in steps and crosswise wooden beams is sufficient. In the upper part, one bracing structure consisting of a wooden beam and a board nailed to it is suspended for each package.
|
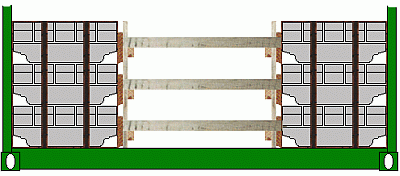 |
|
Bracing of transverse gaps - complicated variant |
With poorly bundled ingots, where there is a risk that individual metal bars could come out of the bundle, bracing must be provided which retains every bar with a wooden member.
In all the bracing structures shown, the crosspieces must be secured against shifting by obliquely placed boards or "X-bracing". The dimensions of the lumber should be determined as a function of the masses to be secured and the necessary residual securing forces according to the rules of thumb stated in the general section.
 |
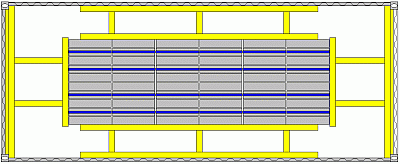 |
|
Bracing of a centrally placed cargo block - plan view |
Stowing a complete block of bundles centrally entails higher material and labor costs. In order to keep such costs within acceptable limits, securing is only provided at floor level in the example.
|
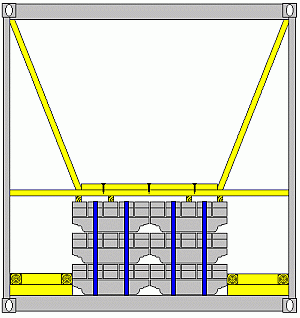 |
|
Securing a cargo block against tipping and vertically - cross-section |
The block can be secured against tipping and vertical stresses by shoring. Lateral securing within the individual layers of cargo is provided by friction due to the pressure exerted by the shoring.
|
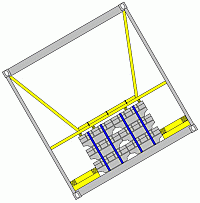 |
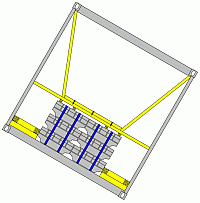 |
|
30° tilt of cargo block |
|
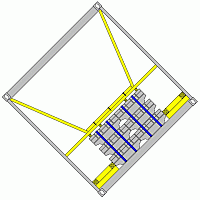 |
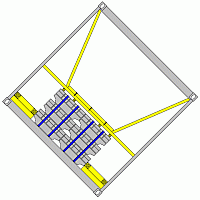 |
|
45° tilt of cargo block |
A properly secured cargo must also be able to withstand a rolling angle of 30° or 45° on board ship.
In terms of labor and material costs, airbags are hard to beat pricewise, but the gaps to be filled in the stow must only be narrow.
|
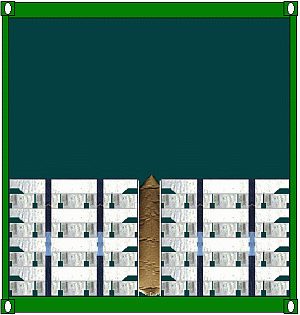 |
|
Aluminum ingots - secured with airbags
|
The aisle left between these aluminum ingots is so narrow that using airbags is feasible. Hardboard or thin sheets of plywood should be placed between the ingots and the airbags. Any airbags used must be secured against slipping out.
|